Quality Management
Quality Improvement Initiatives
Shareholders and Investors, Suppliers and Other Trade Partners, Employees, Global Environment
Basic Approach to Quality
The Sumitomo Riko Group is committed to quality improvement activities under the company-wide quality policy. By establishing a quality assurance system appropriate for a global company, we ensure the high quality and safety of our products.
Sumitomo Riko Group’s Quality Policy
The Sumitomo Riko Group considers it our mission to satisfy our customers and provide attractive products to the world. To fulfill this mission, “All members of the Sumitomo Riko Group are committed to making continuous improvements in pursuit of “Customer First, Quality First” on a global basis. 〜We will become a company trusted by society and customers by establishing Total Quality Management (TQM) activities and S.E.C.Q.-centered business operations.“〜, The above is the Group-wide quality policy, and the Sumitomo Riko Group is working on quality improvement activities.
Approach to quality assurance in the Sumitomo Riko Group
The Sumitomo Riko Group ensures quality by applying the following two approaches in the pursuit of safety and security.
The first is "Ji-Kotei-Kanketsu" (own-process completion). We provide products that can be used with peace of mind through activities that ensure safe products by implementing Ji-Kotei-Kanketsu in each process of product design, production preparation, and mass production (see Fig. 1).
The second is "Quality Governance." Business divisions provide products and services to customers and manage quality risks, and the company-wide Quality Assurance Departments monitor, support, and provide guidance to reduce quality risks so as to ensure the trust of customers and society (See Fig. 2).
The first is "Ji-Kotei-Kanketsu" (own-process completion). We provide products that can be used with peace of mind through activities that ensure safe products by implementing Ji-Kotei-Kanketsu in each process of product design, production preparation, and mass production (see Fig. 1).
The second is "Quality Governance." Business divisions provide products and services to customers and manage quality risks, and the company-wide Quality Assurance Departments monitor, support, and provide guidance to reduce quality risks so as to ensure the trust of customers and society (See Fig. 2).
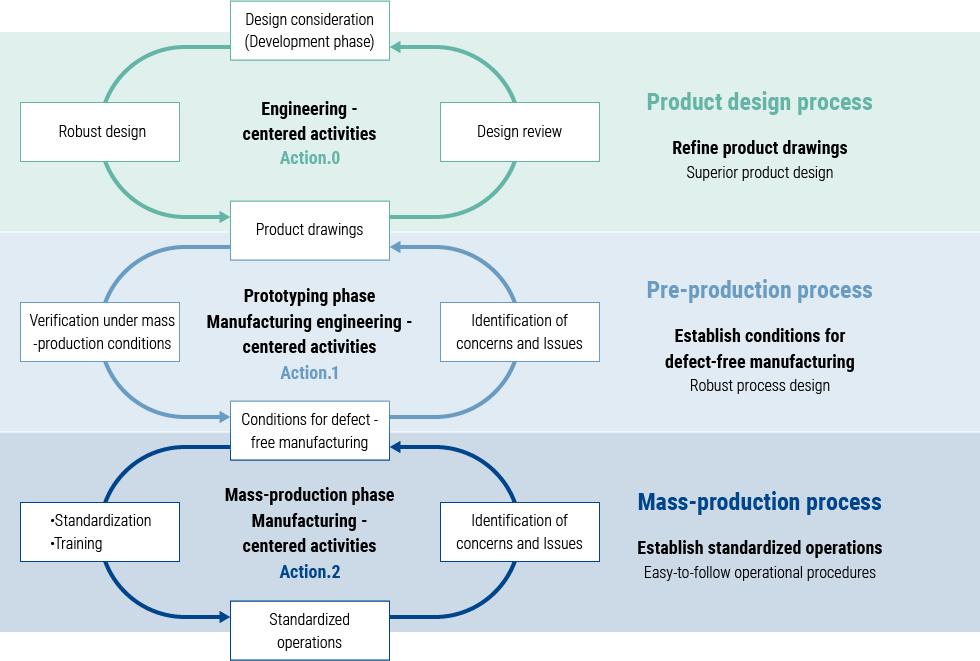
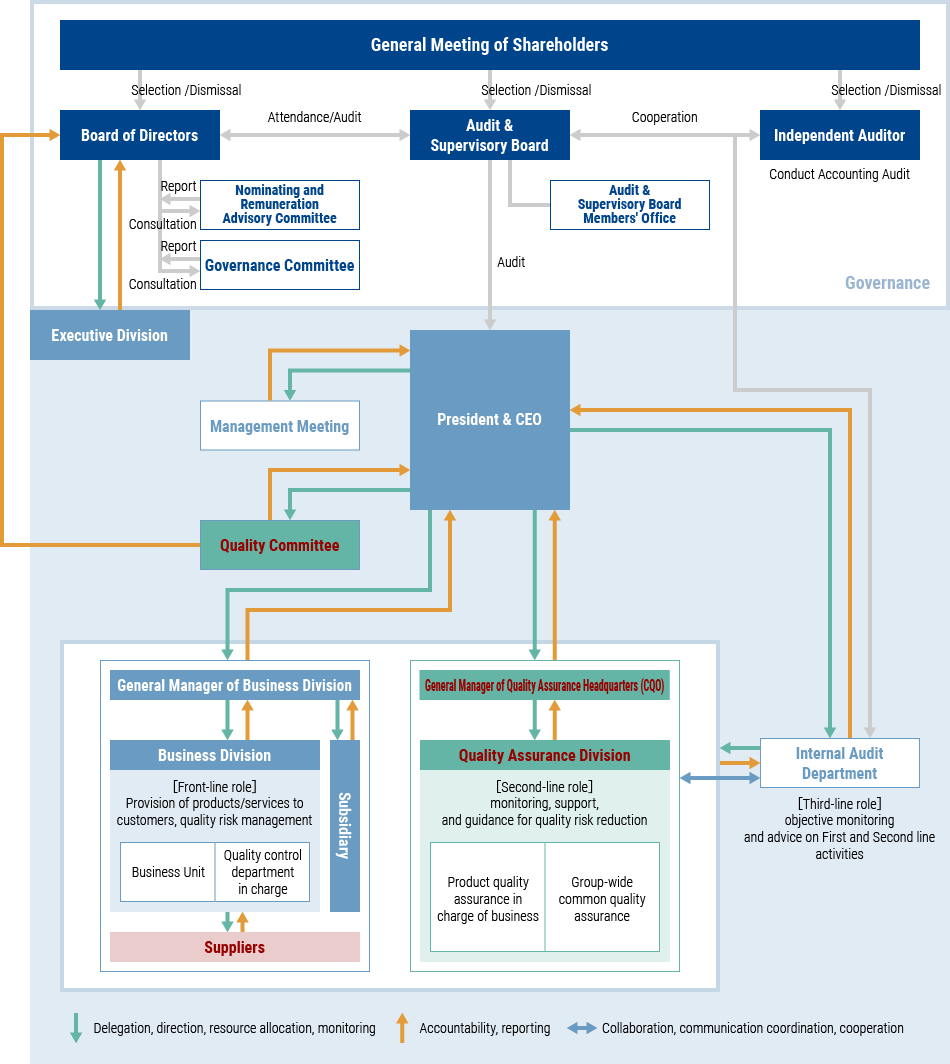
Quality Control Systems
Quality Assurance Systems
In 2016, Sumitomo Riko appointed a Chief Quality Officer (CQO) and established the Quality Assurance Headquarters, integrating the Group's quality functions.
The Quality Assurance Headquarters maintains independence and fairness from the business divisions, and the organizational structure has been designed to raise the quality assurance of the Sumitomo Riko Group to a higher level by strengthening the auditing function and establishing a mechanism to collaborate with the business divisions.
By implementing quality management systems exceeding customer expectations, we are able to supply our customers as well as all other stakeholders with safe, reliable products that offer them peace of mind.
The Quality Assurance Headquarters maintains independence and fairness from the business divisions, and the organizational structure has been designed to raise the quality assurance of the Sumitomo Riko Group to a higher level by strengthening the auditing function and establishing a mechanism to collaborate with the business divisions.
By implementing quality management systems exceeding customer expectations, we are able to supply our customers as well as all other stakeholders with safe, reliable products that offer them peace of mind.
The Quality Committee
The Sumitomo Riko Group has added Quality (Q) to Safety, Environment, and Compliance (S.E.C.), which have been the basis of its business operations since fiscal 2017 onward, changing it to S.E.C.Q. In line with this change, the "Quality Committee" has been established to strengthen the function of monitoring whether quality improvement activities are being carried out.
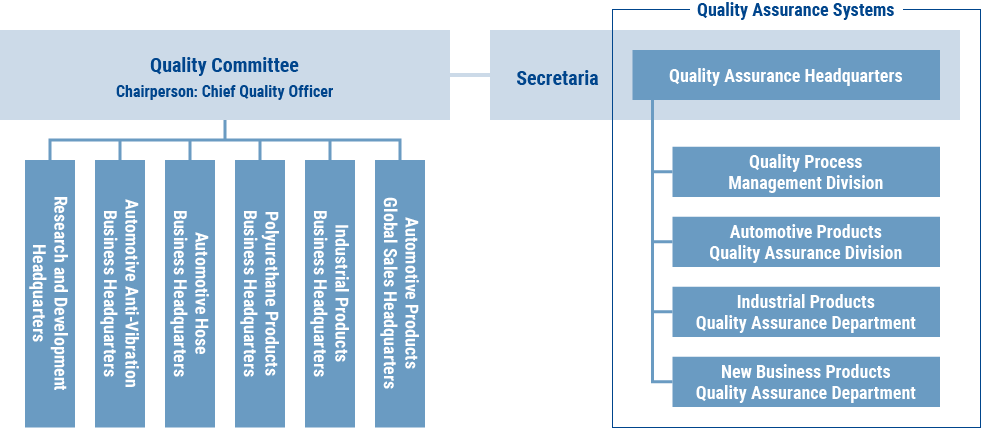
Medium-Term Vision for Quality and Product Safety
The Sumitomo Riko Group will globally promote the following three priority activities to achieve the ideal state of quality toward 2029V.
<The Ideal State of Quality toward 2029V>
- To be known as “Sumitomo Riko of Quality,” which prevents critical quality problems from occurring
- To be a “Sound Company” where no quality compliance problems occur
- To be known as “Sumitomo Riko of Quality,” which prevents critical quality problems from occurring
- To be a “Sound Company” where no quality compliance problems occur
1. Improvement of Product Quality
We will aim to eliminate critical quality problems by promoting the "reliable implementation of recurrence prevention," "thorough verification of change points," and "enhancement of abnormality detection capabilities". We will also build a quality assurance system that extends upstream (research and development) to eliminate defects at the root.
2. Improvement of Operational Quality
We will disseminate the Global Quality Standards (GQS) to all our global bases and establish GQS that are appropriate for new products and new manufacturing methods.
We will also enhance TQM activities in coordination with company-wide DX promotion activities, such as quality education by job level, penetration of small-group activities into the Sumitomo Riko Group, and reinforcement of important themes through the penetration of policy management.
We will also enhance TQM activities in coordination with company-wide DX promotion activities, such as quality education by job level, penetration of small-group activities into the Sumitomo Riko Group, and reinforcement of important themes through the penetration of policy management.
3. Elimination of Quality Compliance Risks
We will regularly conduct quality compliance education, build a system for auditing quality contracts with customers on a global basis, and establish a system to prevent quality fraud by utilizing digitalization and automation.